Deliverable: The parameters required to generate g-code for an operation are entered into the Conversational Wizard.
Here are the parameters needed by the Surfacing (Face Milling) Wizard from G-Wizard Editor:
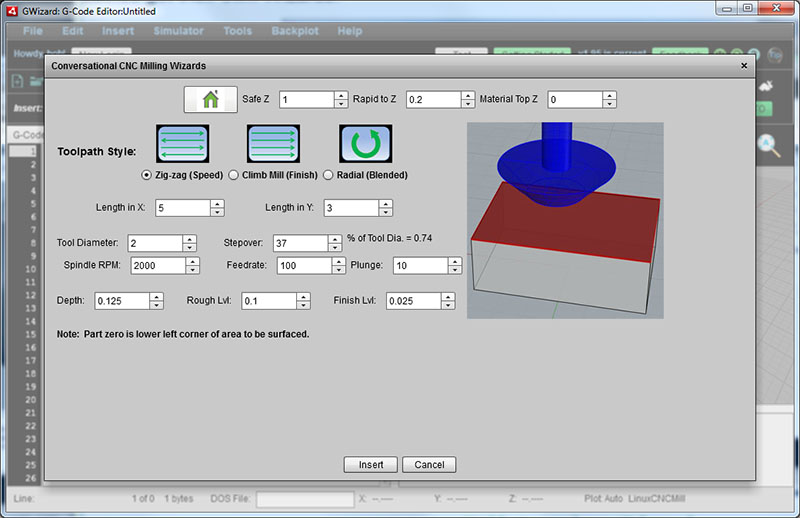
The parameters that must be specified are:
1. Toolpath Style. A graphical icon shows how the face mill will travel across the surface.
2. Safe Z: Z height where the cutter may move at full rapids speed in any direction without hitting anything.
3. Rapid to Z: Z height where the cutter may move at full rapids speed in Z only directly over the cut.
4. Material Top Z: Z height where the cutter will encounter the workpiece. Most CNC'ers like to use 0.
5. Length in X: Length of the area to be surfaced along X axis.
6. Length in Y: Length of the area to be surfaced along Y axis.
7. Tool Diameter: The diameter of the tool that wiill be used.
8. Stepvoer: % of Tool diameter to step over for each pass.
9. Spindle RPM & Feedrate: The Feeds and Speeds to use.
10. Plunge: Feedrate to use for the final plunge down onto the workpiece to start cutting.
11. Rough Lvl: The depth of cut when roughing.
12. Finish Lvl: The depth of cut for the finish pass. The total depth of cut will be Rough Lvl + Finish Lvl
These are all pretty simple questions that are easily answered, even by beginners. To figure out the Feeds and Speeds, use a tool like G-Wizard Feeds and Speeds Calculator.
|